Earlier this week, I discussed progress on the Anchor Edition of Master and Commander. I am grateful for the overwhelmingly positive response. But, as one of the project backers asked, “What about the Victory Edition?” So, here is the other update. I am delighted with the progress of the Victory Edition.
The TL;DR version is that the Victory Edition is, also, nearing completion. I anticipate that it will be completely finished and ready to ship a few weeks after the Anchor Edition. Here is the much longer and, hopefully, more interesting version.
Allowing the Wood to Speak
As I have previously written, the teak planks salvaged from the hull of HMS Victory that arrived at my desert studio were absolutely lovely. They showed complex graining and signs of their previous life.
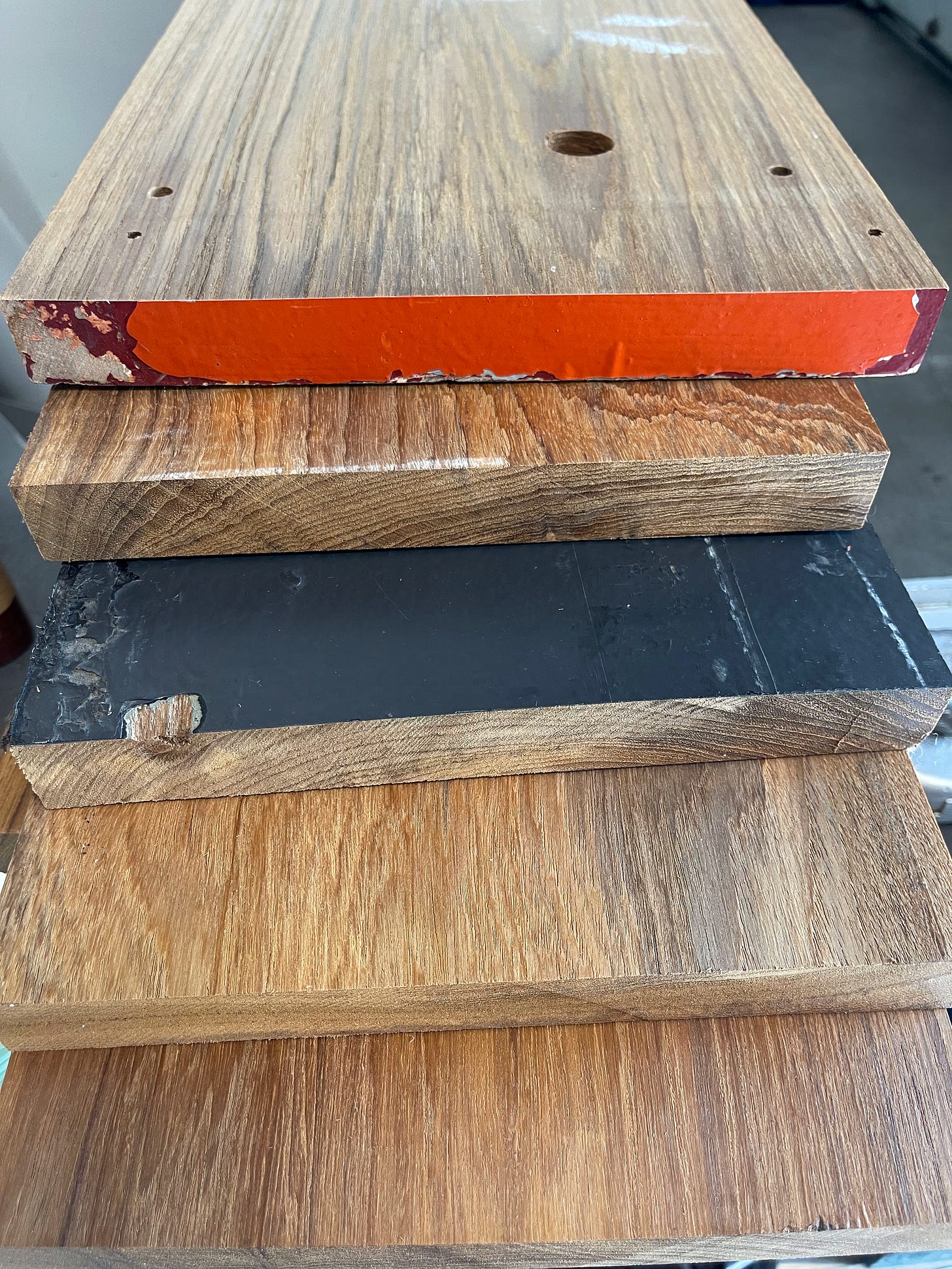
Quickly, I knew that I wanted to simplify the design of the edition, allowing the wood to speak. This has meant a few minor changes. I have eliminated the engraved titles from the front of the cover. The complex graining of the wood made the engraving feel like guiding the lily. Engraving, however, is not eliminated entirely. The inside of the front will feature the official logo of HMS Victory with the Ampersand Book Studio logo engraved on the inner back cover. I think that this will allow the focus to remain on the remarkable Victory wood while still marking its provenance.
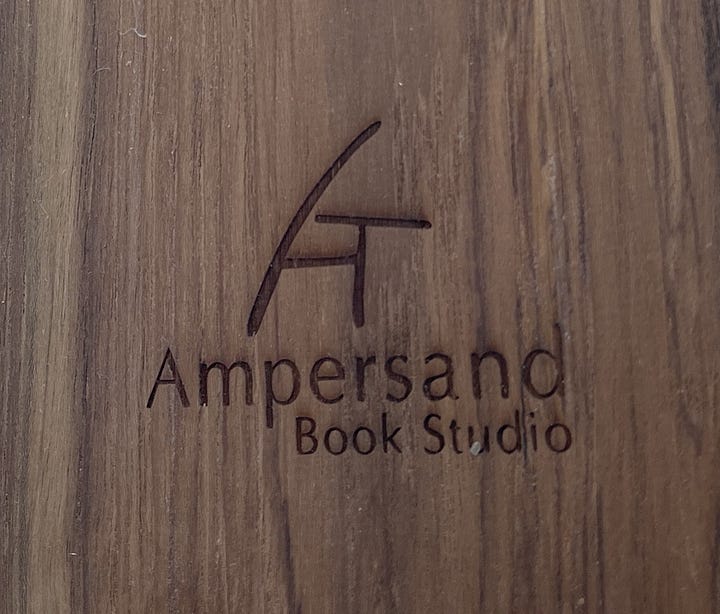
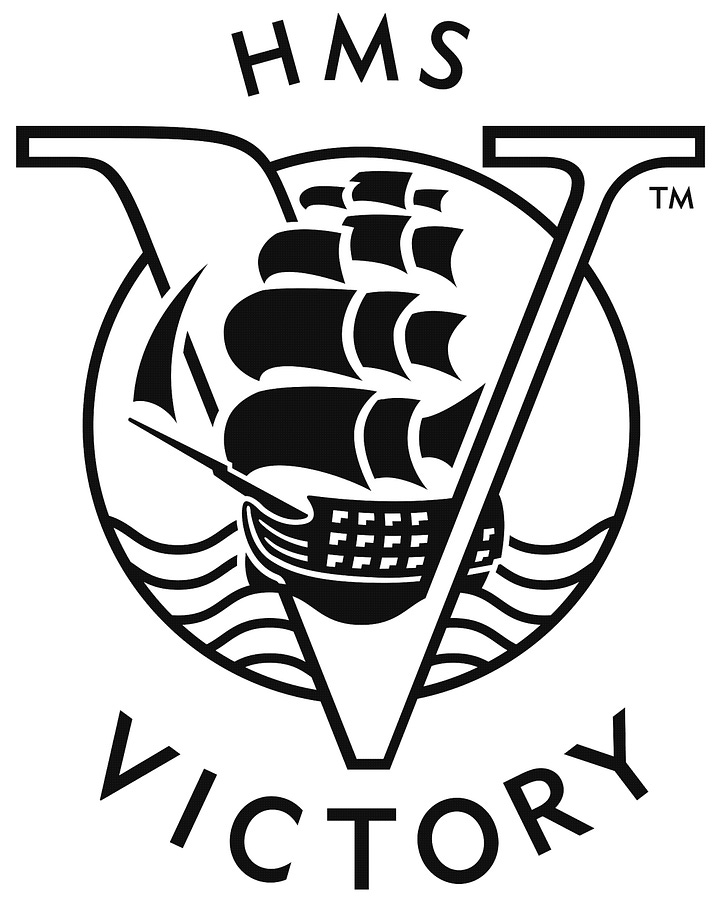
In addition, rather than covering up the wood on the inside of the covers with endpapers, the flax cords that attach the boards to the book will be revealed, highlighting the book’s structure. This is a nod to the nautical nature of the book; after all, wood, cordage, and cloth were the foundation of every sailing ship. It also reflects my “form follows function” aesthetic approach to which I have referred in my posts about the Arts and Crafts Movement and in my rant about fake raised cords.
What this does not mean is the loss of the map of Mahon harbor that is central to the aesthetic of both editions. In the Victory Edition, a fold-out map will be included, harkening back to the inclusion of such maps in the books of the Georgian era.
While these design decisions about the covers were being made, we were also making good progress on the rest of the book. The printed, handmade paper of each copy of the Victory Edition has been sewn onto cords… two-color silk headbands have been meticulously woven (by my trusted sidekick, Emiland, whose fingers are much more nimble than mine)... and they are just awaiting the covers.
Working with the Wood
As previously noted, master woodworker, Dan Eklund, has been working on converting the boards salvaged from Victory into book covers. His first step was to create a prototype – based on my diagram – in 5mm birch plywood. Surprisingly (to me at least), the prototype fit the book perfectly. Holes and slots aligned with the sewn cords of the book block and the thickness was perfect. With a couple of minor tweaks, we were ready to start working with the teak.
Shortly thereafter, Dan began creating a second prototype, this time using the actual teak wood. Each board we received from Victory was about 25mm/1 inch in thickness. Dan had to first saw each board, yielding two – or sometimes three – much thinner boards. Each board was then sent through a planer which brought the thickness to just over 5mm. Final sanding would find them at the perfect thickness for the covers of our book.
When I visited Dan’s workshop to see the first teak prototype, I was absolutely delighted by the results of his work. Although they were not a finely finished version, the covers looked great and fit perfectly with the book structure. Dan had the go-ahead to start producing the final covers of the book. Or so we thought.
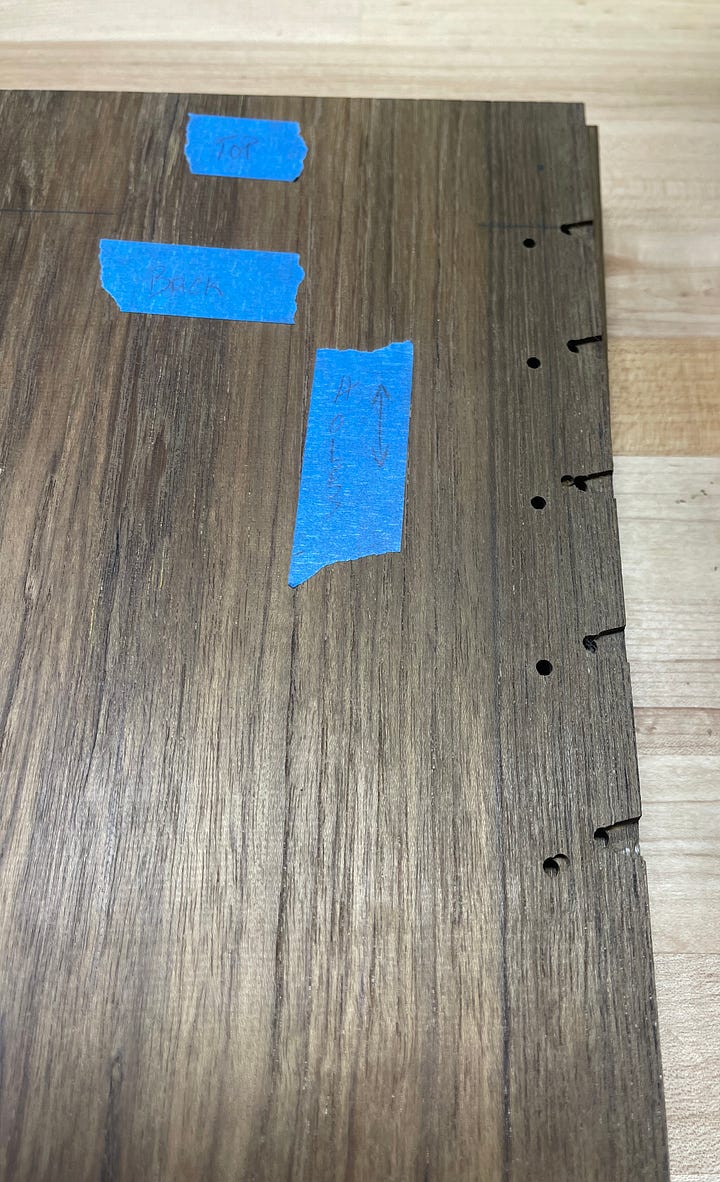
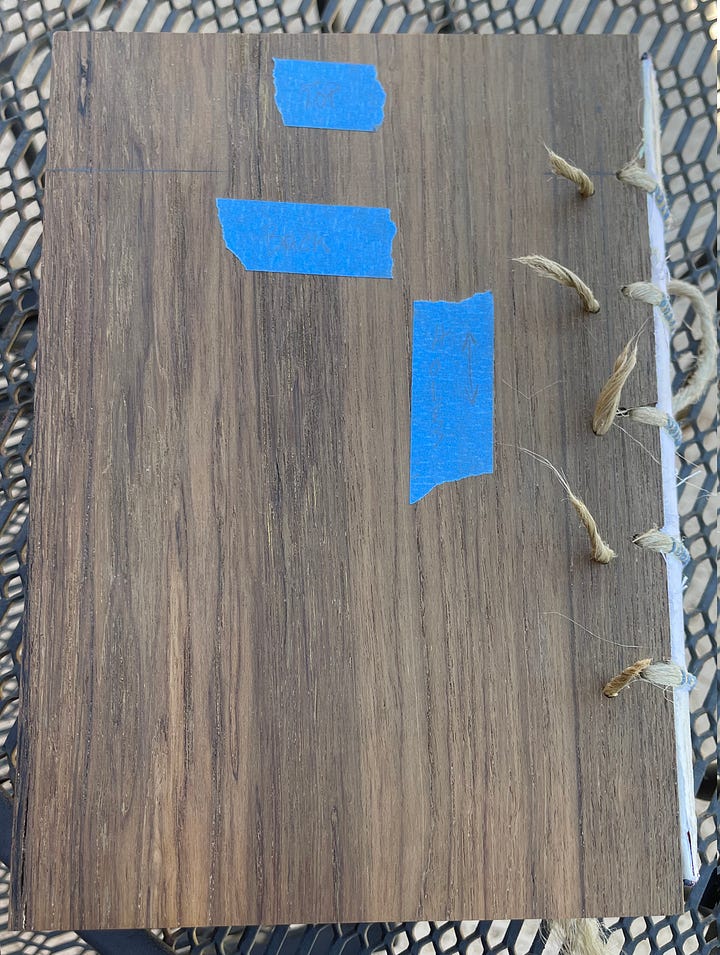
When he started to mill the rest of teak to the thickness for the book covers – 5mm ±0.5mm – the first boards warped. Indeed, you can see that happening in the following video; as soon as the thinner board detaches, it almost immediately twists and warps.
It turns out that after a long life as part of the hull of the ship – following the curvature of the hull and exposed to sea water – the boards really wanted to return to their somewhat curved stasis. Although the warping was not massive, he and I thought that it would be noticeable on the books. So, we set out to explore options.
The first idea was to make the covers thicker (8-10mm or so). Such thick covers were quite common when wood was used to create medieval books. This “cut-away” binding (below) by the remarkable Karen Hanmer (about whom I have previously written) shows the thickness of such historic bindings. Indeed, these are nowhere near the thickness of some bindings of the era.
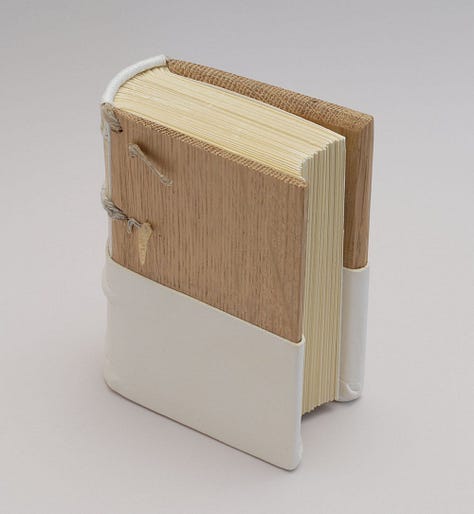
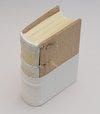
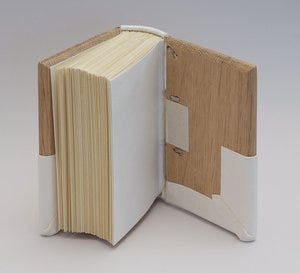
However, Master and Commander is not a work of medieval literature. Thick covers would alter the design of the book too much, creating covers that were out of proportion.
Instead, Dan proposed that we stabilize the wood using a complex process that employs a vacuum chamber, a stabilizing resin, and heat. Essentially, the wood is submerged in a pool of stabilizing resin. The wood and resin are then placed under vacuum, eliminating air from the pores of the wood. Once the vacuum is released, the resin fills the voids, replacing the air. The wood is then placed in an oven set at a very low temperature to cure the resin and stabilize the wood. The process does not change the color, texture, or aroma of the wood. It does, however, make the wood more stable and less susceptible to atmospheric changes and warpage. All of this had to be undertaken in small batches as large vacuum chambers cost many, many thousands of dollars. While this slowed our process a bit, it has led to a great outcome.
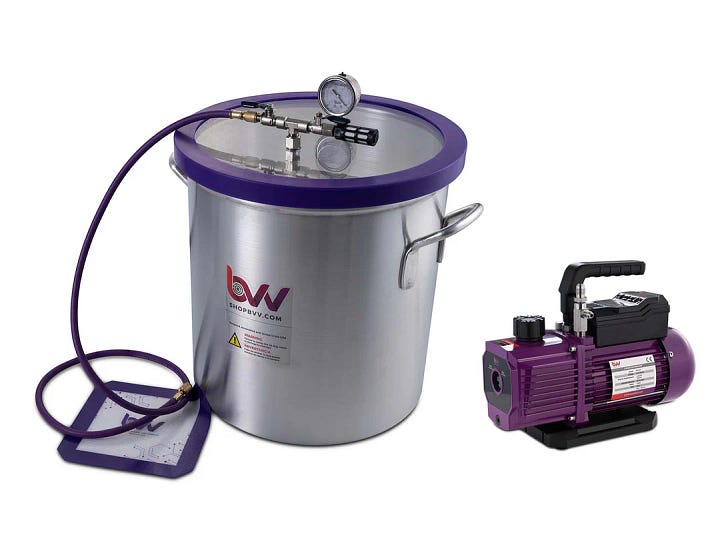
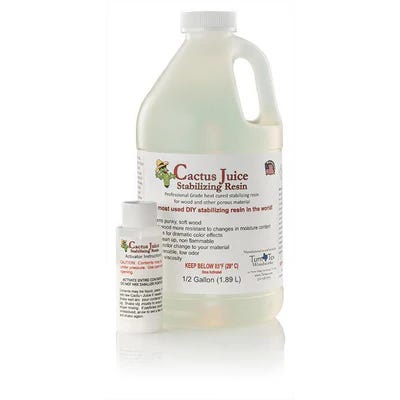
This past weekend, after all of the wood had been stabilized but before the final milling and finishing could take place, Dan and I got together to match the front and back boards for each copy of the book. The original planks I acquired from Victory exhibited significant differences in grain and color, not only when comparing one to the next, but even over the length of the individual board. We did our best to match them to create a cohesive look for each copy of the book.
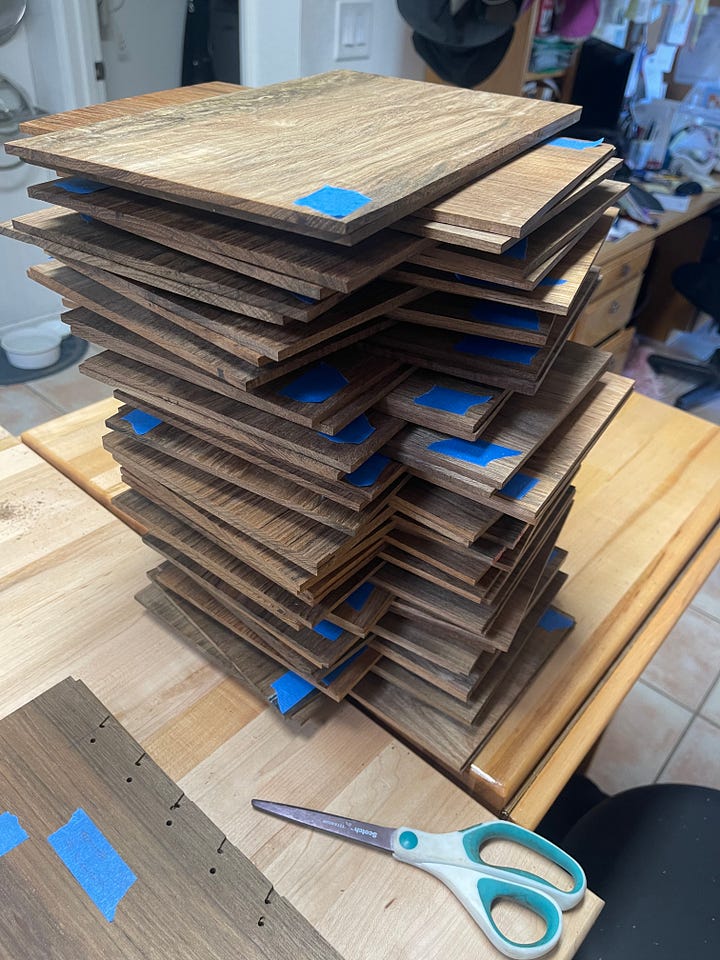
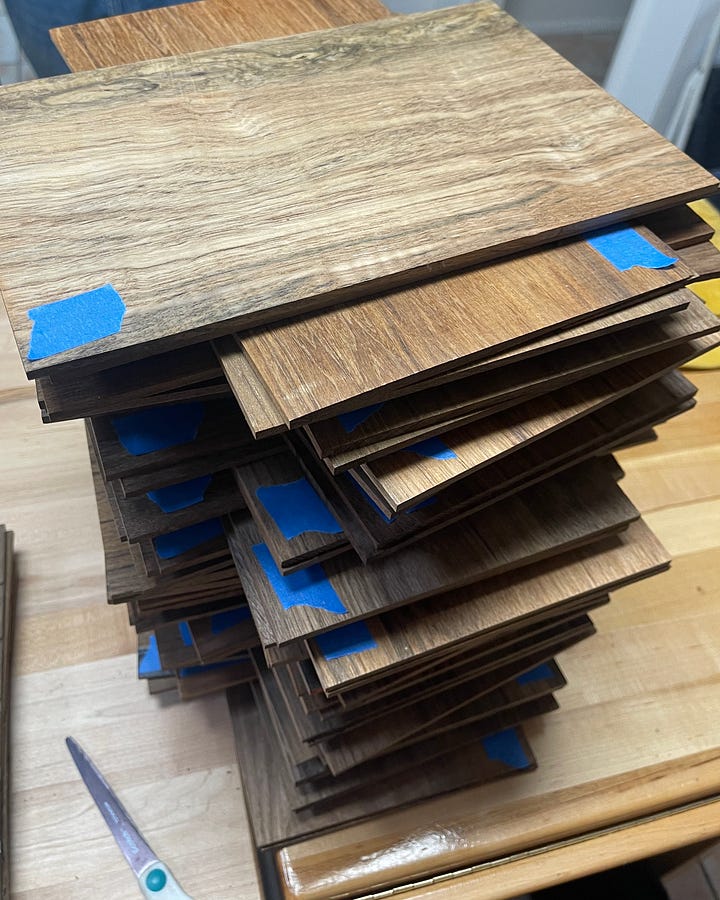
Over the next few weeks, Dan will finish the boards… drilling the holes and creating the slots through which the cords will pass to attach the covers… laser engraving the logo of HMS Victory and Ampersand Book Studio on the inside of the covers... and applying a natural wax finish.
By the time the Anchor Edition is completed, the covers should be ready. Then the process of completing the Victory Edition should go very quickly.
I cannot express how excited I am to bring the Victory Edition to fruition.
Victory Wood Boxes
For the lucky few who ordered a custom wood box for their copy of the Victory Edition, I have big news from Scotland: the boxes are finished! They will soon be shipped to my studio.
Made by Callum and David Robinson, each box combines teak salvaged from HMS Victory and English oak. The top features a hand-carved image of a man-of-war. I will share photos once they arrive safely here in the Sonoran Desert. My profound thanks go to Callum and David for their passion and artistry.
Can you tell us when you expect to ship the Victory edition?
As much as the engraved titles were elegant, showing off the wood for itself seems very appropriate. I especially love the touch of adding the Victory’s insignia.